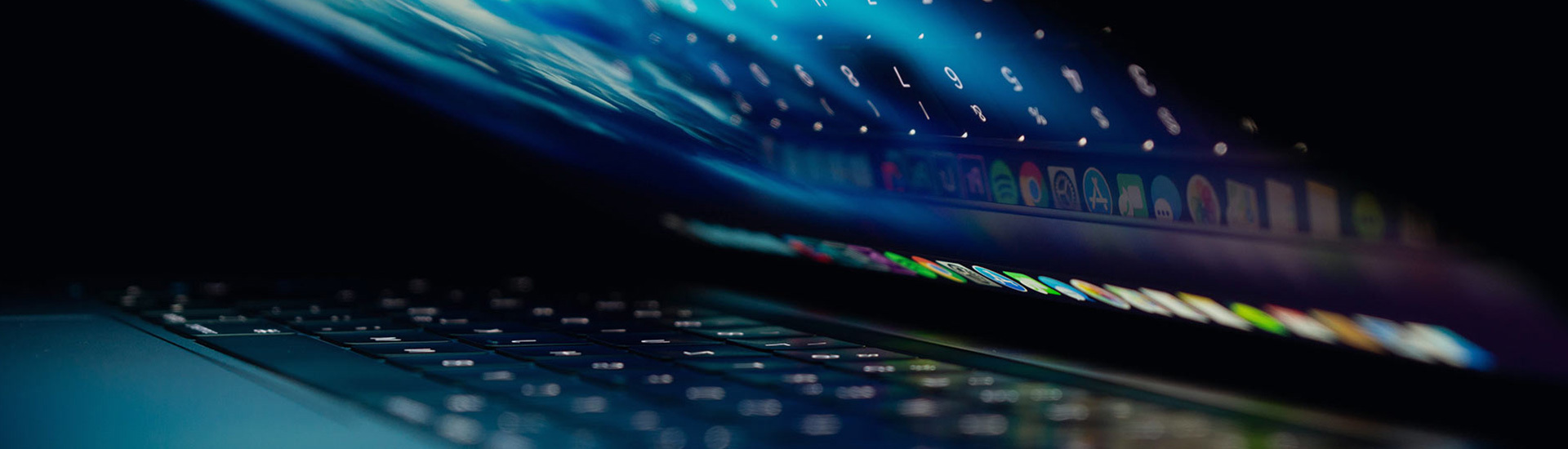
News
Quality Control of High Quality Zinc Alloy Die Castings
Release time: 2022-06-08
Quality Control of High Quality Zinc Alloy Die Castings
The quality requirements of zinc alloy die-casting electroplating products in North America and Europe markets shall meet the requirements of ASTMG85 standard for passing the 48 hour acid salt spray (Grade 10) defect free test. This brings great difficulty to the quality control of zinc alloy die-casting electroplating. Requirements can be achieved by controlling the following factors:
1、 Quality requirements for die casting blanks:
1. Purchase high-quality zinc ingots, store them dry and clean, and do not mix the stripped products and dirty water into smelting.
2. The die casting blank shall be free of material shortage, deformation, shrinkage, blistering, peeling, interlayer, crack, pore and flash.
3. The surface is clean and free of oil stain and collision scar.
4. Castings shall be baked in 150 ℃ oven for 1 hour without bubbles. 5. The depth from the subcutaneous pinhole to the polished surface must be greater than 0.30mm. 6. The density of polished parts is greater than 6.58g/cm3.
2、 The control of polishing is also critical:
1. It shall be polished separately and shall not be on the same site and polishing materials as the copper parts. If there are a large number of copper atoms left on the workpiece surface, because it is the external force of polishing that invades it, the copper atoms and the zinc matrix are mechanically bonded without diffusion and mutual compatibility. When alkaline copper is plated, the bonding force between the coating and the matrix and the structure of the coating itself must be affected, thus reducing the corrosion resistance.
2. The red paste is used for rough polishing, and the white paste is used for bright polishing, without missing polishing, leaving no blank mark, and the surface is full without depression, bump, pinhole, and black spot.
3. Frequently wax the workpiece, with a small amount of wax, and do not polish it vigorously to avoid dense holes caused by high temperature burns on the workpiece surface.
4. Do not over polish, and the allowance shall be controlled within 0.10. It is not allowed to throw away the dense layer to expose the dense needle holes.
5. It shall be placed separately in a dry and clean place without collision, avoiding surface oxidation and hydration, and electroplating shall be carried out as soon as possible after throwing.
3、 The shallow gas (needle) hole under the skin is the main stubborn defect that affects the electroplating quality (rate) of zinc alloy die castings.
It is still impossible to completely eliminate the pores and pinholes according to the die-casting technology capability of the current market. What can be controlled is that the pores (pinholes) become thinner, more dispersed, and deeper subcutaneously. The detectability of the subcutaneous pinholes is poor, and they are often checked by naked eyes after polishing. This requires the inspectors to have a high level of professionalism and insight, and analyze relevant theories according to the failure mode, The detectability of visual inspection is only 0.5 at most. This is its basic and main character. When the subcutaneous pores or pinholes are relatively dispersed, smaller and deeper (such as below 0.50), the impact on the quality of the electroplating layer is also small. When the subcutaneous air hole or pinhole is slightly larger, the size is general (such as less than 0.20mm), and it is not very shallow (such as about 0.20mm), it can be polished once again after being coated with acid copper, the dent can be polished, the rough surface structure can be removed, and then nickel and chromium plating can be carried out. It can also pass the 48 hour acid salt spray test, so as to improve the utilization rate of die castings. The fact that ordinary subcutaneous pores and pinholes can also produce some qualified products covers some of the hazards of subcutaneous pores and pinholes, which constitutes obstinacy.
4、 The bottom layer copper plating adopts the process of copper plating plus pyrophosphate copper plating plus salt bright copper plating.
Semi bright nickel plating processes such as semi bright nickel+bright nickel+nickel sealing are selected. Semi bright nickel: appropriate sulfur free brightener is added to Watt nickel bath with good conductivity and covering ability to form a semi bright nickel plating bath, and an appropriate potential difference (80mv~130mv) is generated between the semi bright nickel bath and the bright nickel layer to achieve electrochemical protection. The film thickness of semi bright nickel layer can be controlled at 2/3 of the total film thickness (about 10 μ M) is ideal. Bright nickel: the film thickness accounts for about 1/3 of the total nickel layer thickness (i.e. 5 μ M). The potential difference between the two layers makes the double layer nickel from the longitudinal corrosion of single layer nickel to the transverse corrosion, so as to protect the copper layer and the zinc alloy substrate below. Nickel sealing: add some non-conductive particles with a diameter of 0.1~1 in the common bright nickel solution μ M (micron) insoluble solids such as SiO2 are suspended in the plating solution by stirring. With the help of an appropriate codeposition accelerator, these particles can codeposition with nickel to form a composite coating composed of nickel and particles. In the subsequent chromium plating, because the particles on the surface of the composite coating are not conductive, chromium can not be deposited on the surface of the particles, resulting in the formation of a large number of micropores on the chromium layer, which is called microporous chromium. The particle density of nickel seal layer is ideal at 15000~30000/cm2. A large number of micropores on the surface of microporous chromium can largely eliminate the internal stress in the ordinary chromium layer, thus reducing the stress corrosion of the chromium layer. Particularly important is that a large number of micropores on the chromium layer expose the bright nickel under the chromium layer in a large area. Under the effect of the corrosive medium, chromium and nickel form a battery, the chromium layer is the cathode, and the bright nickel exposed at the micropores is the anode, which causes corrosion. Thus, the corrosion mode of large cathode and small anode is changed, so that the corrosion current is almost dispersed on the entire bright nickel layer, thus preventing the generation of large and deep corrosion grooves and pits that are straight through the base metal, reducing the corrosion rate of the coating, and developing laterally, thereby protecting the base and significantly improving the corrosion resistance of the coating.