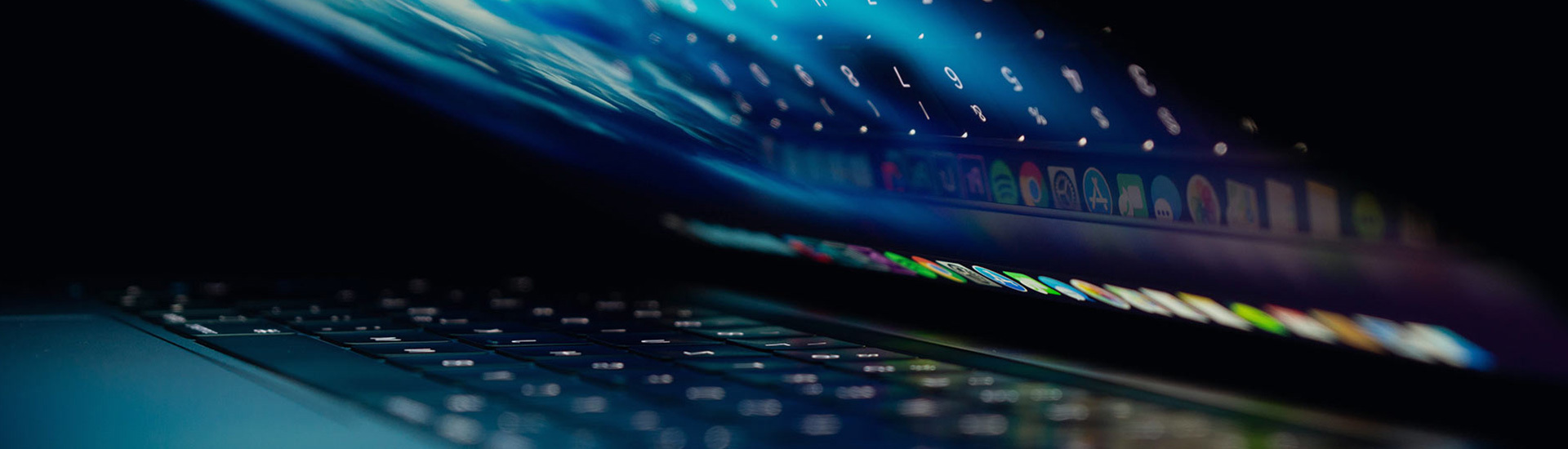
News
Prevention of Surface Defects of Aluminum Alloy Die Castings
Release time: 2018-06-04
With the gradual emergence of the advantages of aluminum alloy die castings, the market demand constantly requires the processing plant to increase production, so as to upgrade the old iron castings to aluminum alloy or magnesium alloy as soon as possible. As a result, the task of the processing plant is heavier, and the quality must also be adhered to. Today's editor will teach us how to prevent some common defects of aluminum alloy die castings.
1、 Drawing die
Characteristics and inspection method. The other is that the liquid metal adheres to the mold, causing strain, resulting in excessive or insufficient material on the surface of the casting.
Causes: 1. The cavity surface is damaged (collapsed or knocked). 2. The inclination of the demoulding direction is too small or inverted. 3. The ejection is unbalanced and deviated. 4. Too high pouring temperature and too high mold temperature lead to adhesion of alloy liquid. 5. The mold release agent has poor effect. 6. The iron content of aluminum and gold components is less than 0.6%. 7. The cavity is rough and not smooth, and the hardness of the mold is low.
Precautionary measures: 1. Modify the damaged part of the mold surface, modify the demoulding slope, advance mold hardness (HRC45 °~48 °), and advance mold finish. 2. Adjust the ejector rod to balance the ejection. 3. Replace the mold release agent with good mold release effect. 4. Adjust the iron content of the alloy. 5. Lower the pouring temperature and control the mold temperature to be stable and balanced. 6. Adjust the direction of the inner gate to avoid the metal liquid directly impacting the core and wall.
2、 Bubble
Characteristics and inspection method: There are arches of different sizes on the surface of the casting, or there are subcutaneous cavities.
Causes: 1. The filling degree of metal liquid in the injection chamber is too low (controlled at 45%~70%), which is easy to produce entrainment, and the initial injection speed is too high. 2. The mold pouring system is unreasonable and the exhaust is poor. 3. The smelting temperature is too high, the gas content is high, and the molten liquid is not degassed. 4. The mold temperature is too high, the mold retention time is not allowed, the metal condensation time is insufficient, the strength cannot be opened too early, and the pressurized gas expands. 5. Excessive amount of mold release agent and injection head oil. 6. The blowing time is too short after spraying, and the mold surface water is not dried.
Preventive measures: 1. Adjust the switching point of die-casting process parameters, injection speed and high-pressure injection speed. 2. Modify the mold runner and add overflow groove and exhaust groove. 3. Lower the mold temperature in the defect area, and then lower the pressure effect of the gas. 4. Adjust the smelting process. 5. Extend the mold retention time and adjust the air blowing time after spraying. 6. Adjust the amount of release agent and injection oil.
3、 Crack
Characteristics and inspection methods: The surface of the casting has linear or irregular narrow texture, which has a development trend under the action of external force. Cold cracking - The metal at the crack is not oxidized. Hot cracking - where the metal is oxidized.
Causes: 1. The iron content in the alloy is too high or the silicon content is too low. 2. The content of harmful impurities in the alloy is too high, which reduces the plasticity of the alloy. 3. Aluminum silicon alloy: aluminum silicon copper alloy contains zinc or copper content is too high; There is too much magnesium in aluminum magnesium alloy. 4. The mold temperature is too low. 5. The wall thickness of the casting changes dramatically and the shrinkage is blocked. 6. Too long mold retention time and high stress. 7. The force is uneven during ejection.
Preventive measures: 1. Correctly control the alloy composition. In some cases, pure aluminum ingots can be added to the alloy to reduce the magnesium content in the alloy; Or the content of silicon before adding aluminum silicon center alloy into the alloy. 2. Change the casting structure, increase the fillet, increase the demoulding angle, and reduce the wall thickness difference. 3. Change or increase the ejection direction to make the ejection force uniform. 4. Shorten mold opening or core pulling time. 5. Forward mold temperature (mold working temperature 180 ° - 280 °).
4、 Deformation
Characteristics and inspection method: the geometric shape of the die casting is inconsistent with the drawing. Total or partial deformation.
Causes: 1. Poor design of casting structure causes uneven shrinkage. 2. The mold is opened too early, and the casting cannot be rigid. 3. The drawing die is deformed. 4. The setting of ejector rod is unreasonable, and the force is uneven when ejecting. 5. Improper gate removal method.
Preventive measures: 1. Improve the casting structure. 2. Adjust the mold opening time. 3. Reasonably set the position and quantity of ejector pin. 4. Select reasonable gate removal method. 5. Eliminate die elements.
5、 Marks and stripes
Characteristics and inspection method.
Causes: 1. The trace left after the metal liquid that first enters the mold cavity forms an extremely thin and incomplete metal layer and is compensated by the later metal liquid. 2. The mold temperature is too low. 3. Spatter is caused by too small sectional area of inner gate and improper orientation. 4. The pressure acting on the liquid metal is insufficient. 5. Speckle: Too much paint and injection oil.
Precautionary measures: 1. Temperature of advance die. 2. Adjust the section area or orientation of the ingate. 3. Adjust the liquid metal speed and pressure of the ingate. 4. Select appropriate paint, injection oil and adjust the amount of paint injection oil.