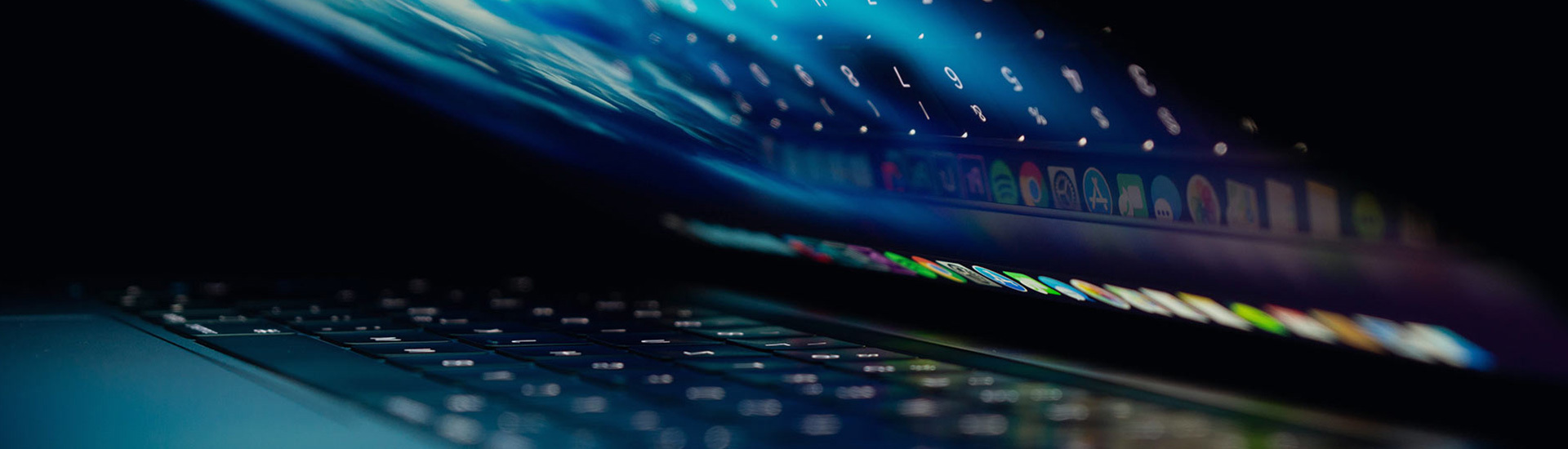
News
Causes and solutions of unqualified zinc alloy die castings
Release time: 2018-02-07
Foaming causes of zinc alloy die casting:
1. Caused by pores: mainly due to pores and shrinkage mechanism. The pores are usually round, but most of the shrinkage is irregular. (1) Cause of air hole: In the process of inflation and curing, due to gas invasion, metal liquid will produce air holes on the surface or inside of the casting. B Invasion of volatile gas from paint. C The gas content of alloy liquid is too high, and it is coagulated and precipitated. When the mold exhaust is poor, the gas in the cavity and the volatile gas of the paint will eventually remain in the formation of the casting porosity. (2) Reasons for shrinkage: During the solidification of liquid metal, due to the volume reduction or the final curing part is not liquid metal material and shrinkage pores. B. The uneven thickness of the casting or casting is locally overheated, which causes the surface to solidify slowly and form a concave surface when the volume shrinks. Due to the existence of air holes and shrinkage holes, when the die casting surface can enter water painting and electroplating, the gas in the hole will expand thermally, or the water in the hole will become steam and expand in volume, resulting in bubbles on the casting surface.
2. Intergranular corrosion of harmful impurities in zinc alloy: lead, cadmium and tin will gather at the crystal boundary, leading to intergranular corrosion, intergranular corrosion and breakage of metal substrate and coating, accelerating the disaster. The intergranular corrosion in this area will expand the top, causing bubbles on the casting surface. Especially in humid environment, intergranular corrosion will make castings deformed, cracked, or even broken.
3. Causes of cracks: water, cold insulation wire and hot cracks. 1) Water and cold partition line: during the charging process of metal liquid, the metal liquid enters the contact wall and solidifies prematurely, then the liquid metal and metal solidification can be integrated, and strip defects appear in the joint form of the casting surface. The water is usually shallow on the surface of the casting, and the cold partition may penetrate into the casting. 2) Hot crack: when the wall thickness of the casting is uneven, the stress will produce a curing process; B The metal strength is insufficient due to premature ejection; C The mold temperature is high, the jacking force is uneven, and the grains are coarse; E Presence of harmful impurities. These parameters may be cracked. When the die casting has water lines, cold separation lines, hot cracks and plating solution, the cracks will penetrate and transform into steam baking, and the metal will deposit on the top to form bubbles.
Methods to solve the defects of zinc alloy die casting:
1. Control of pore formation: the key is to reduce the amount of casting mixture. The ideal metal flow rate should be continuously accelerated into the mold cavity through the splitter cone and pouring channel to form a smooth metal flow direction. The design of conical flow channel is adopted, that is, the pouring flow shall continuously accelerate the gradual decrease from the nozzle to the pouring port, so as to achieve this goal. In the filling system, the mixed gas forms pores due to the mixing of turbulence and metal liquid. The liquid metal in the simulation die casting process in which the gating system enters the mold cavity obviously increases the change of the gating port of the flow channel, making the metal liquid flow turbulent and entrained. The liquid metal is smooth, which is conducive to the gas entering the overflow tank and exhaust tank from the gating port and cavity.
2. Shrinkage: make all parts of zinc alloy die-casting castings as far as possible, and uniformly heat dissipation and curing. Shrinkage can be avoided through reasonable nozzle design, mold design, gate thickness and position, mold temperature control and cooling. Intergranular corrosion: control the main impurity content of harmful alloy materials, especially 0.003% lead. Pay attention to waste and impurities.
3. Water and cold insulation: it can increase the mold temperature, increase the inner gate speed, or increase the overflow groove in the cold insulation area to reduce the cold appearance and close the grain.
4. Hot cracks: the thickness of zinc alloy die castings changes slowly, reducing the generation of stress; Die casting process parameters and adjustment; Lower the mold temperature.